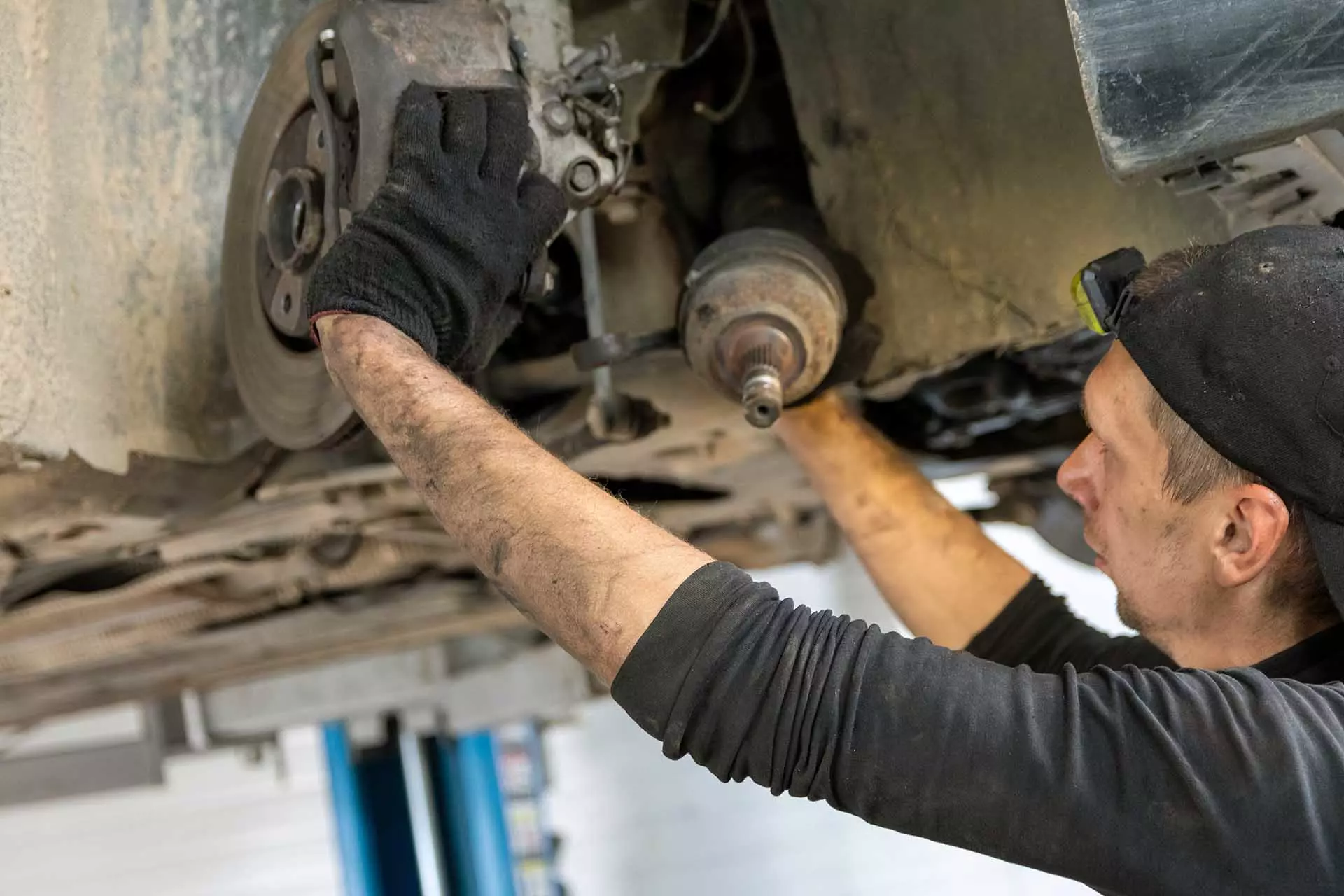
How much does it cost to replace a drive shaft?
Drive shaft
£200-£1000
How much could I save by replacing my own drive shaft?
If you have a supermini such as a Fiat 500 or Ford Fiesta, you could be looking at £200-£300, purely for the parts – your Haynes Manual will guide you through the drive shaft replacement procedure, step by step.
Drive shafts for larger cars, such as the Ford Focus, VW Golf and Vauxhall Astra, cost a bit more, while those for sports cars can easily exceed £1000. This is because drive shafts are heavy, complicated pieces of kit that are built to transfer torque from the gearbox to the wheels – they need to be sturdy.
With these costs in mind, it's not hard to understand why you'd want to fit the new drive shaft yourself instead of paying a garage up to around £400 in labour fees to do it for you.
Find a manual for your car here and start saving with Haynes
How does a drive shaft work?
A car's drive shafts are vital components. Your engine and gearbox are the dream team, but if all their good work can’t get to the wheels, it’s all in vain.
Drive shafts are charged with the task of handling potentially huge amounts of torque, which means they fail over time. They can break suddenly, the splines can shear off bit by bit, or you may even bend one if you hit something particularly unforgiving.
If any of that happens, you'll either have to leave the car where it is and get it trailered home or, if it's driveable, tend to it as soon as possible.
Changing a drive shaft is actually a simple task that a home mechanic can undertake without too much trepidation. It’s just a case of being thorough, being safe, and of course having your trusty Haynes Manual to hand.
5 signs of a failing drive shaft
A bad driveshaft can sometimes be very difficult to diagnose if it's in the early stages of failing, but imminent drive shaft failure should be more obvious. Here are some symptoms to keep an eye and ear out for when diagnosing drive shaft problems:
Vibrations
Can you feel a slight shake through the steering wheel or is it more of a seat-of-your-pants thing, where the shaking is making itself felt via the driver's seat? Vibrations are often caused by a wheel that's thrown a balance but can also be a sign of a drive shaft problem.
Clunking
Worn drive shaft joints can cause a loud clunking, which usually appears suddenly rather than getting louder over time.
Clicking when turning
This failing driveshaft symptom is quite distinctive and only makes itself heard when you're making a right or left (or both) turn, with the wheels at an angle. This is a sure sign of a worn CV joint. Ignore this at your peril because further wear will stop the wheels from turning smoothing, potentially upsetting the car's handling.
Juddering when accelerating
This unusual symptom is a sign of universal joint or bearing issues. It can occur when you're moving off from a standstill or even from a low speed.
Squeaking
Your drive shaft's joints are usually packed with grease to keep friction to a minimum. But if the rubber gaiters (shown below) that hold the grease in place become damaged, the grease will leak out and grit and grime will get in. That's very bad news for moving parts because they'll wear out faster.
Underbody squeaks when you're on the move are likely to indicate that your gaiters need to be replaced.
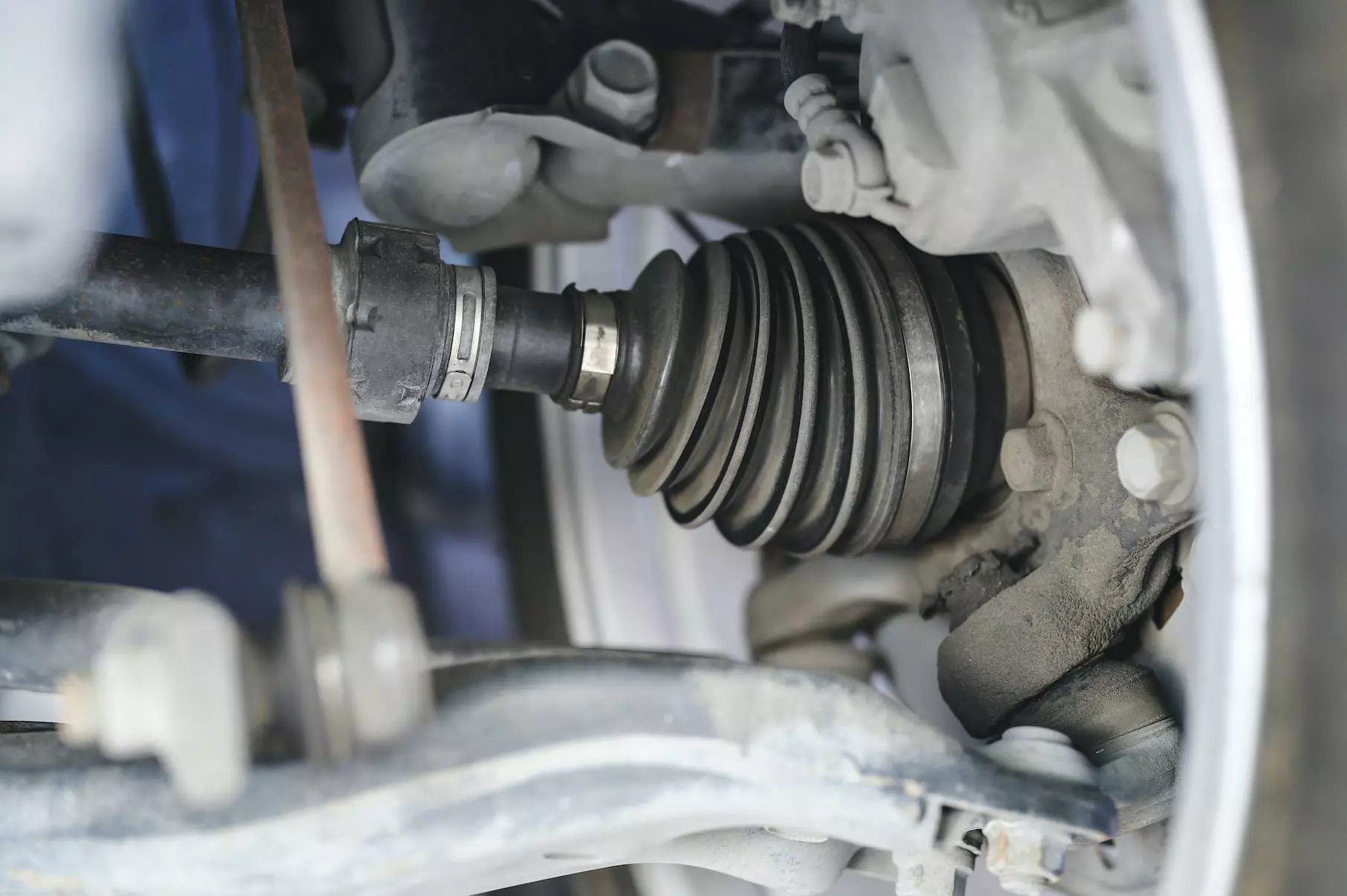
How to change your drive shaft
This is a basic explanation of the procedure for renewing a drive shaft on a typical front-wheel-drive vehicle. Your Haynes Manual goes into full detail for your model.
1. Crack the hubs
While there is weight on the car, remove the split pin from the hub nut, then crack the hub nut off so that it’s loose. Don’t take it all the way off though. It will be a big nut, approximately 30mm, so you’ll need the right socket. And you’ll need a lot of effort because they can be torqued to over 250Nm.
2. Jack the car up
You’re not doing anything with the car on the floor, so get it jacked up and on axle stands. The stands are not only for safety reasons here, you also need the wheels to be in the air - ramps won’t be any use here.
3. Wheels and brakes
Take the wheels off, put them under the car for safety and then start on the brakes. You’re going to need to remove the caliper, but you won’t need to disconnect the brake line. Use some sturdy cable ties or metal wire to suspend the caliper so there is no weight/tension on the brake hose.
4. Hubs
Now you can free off and remove the hub nut completely. At this stage, you may also want to remove the brake disc – you don’t always have to, but it takes 20 seconds and makes for better access.
5. Lower ball joint
Undo the nut onto the lower ball joint and then with the aid of a ball joint splitter, break the hub assembly and the lower arm apart. You should now be able to pull the hub away from the drive shaft, freeing the outermost end. In some cases (and this is where your Haynes Manual comes in) you may need to remove the anti-roll bar.
6. Gearbox end
The end of the shaft that goes into the gearbox will either slide right out, or it will need some gentle persuasion due it being held in by a circlip. Consult your Haynes Manual before yanking it too much and breaking it.
7. Now go in reverse
To fit the new drive shaft, just follow the above steps in reverse. Can't get the drive shaft back in? After making sure the splines are correctly lined up, tapping it with a rubber mallet should persuade it to install correctly. Job done! Make sure you tighten the hub nuts up to the manufacturer's specified torque, which you'll find in the Haynes Manual or AutoFix.














Drive shafts: how long do they last?
A car's drive shafts are exceptionally important, given that they take the power from the engine and send it to your wheels.
Despite their importance though, drive shafts are not a service part, and this means there is no set interval for when they should be changed. Every car is different. The key to drive shaft longevity is preventative maintenance as well as just generally looking after them.
If you look after your drive shafts, they can last the lifetime of the car. It only if you ignore the information below that they can become a problem.
The main shaft of the drive shaft unit is just a bar of metal, and as such is pretty robust. The only way this bit fails is if it’s damaged, or if the rust is allowed to eat it away. As such, there is no harm in getting under your car with a wire brush, clean up the shaft and give it a new coat of rustproof paint. This will extend the life no end.
Other than that, there are two main points of driveshaft failure. They are:
The splined ends
Each end of the drive shaft has a splined input piece. It is these splines that allow the drive shaft to be acted upon by the gearbox, while at the other end, they allow the shaft to act on the wheel/hub, thus delivering power.
If these splines are damaged, the shaft can start to break up and shift, meaning the power isn’t delivered. In situ, these spines are pretty hardy.
However, if the car is driven hard, this can damage them. Also, if the car is modified to produce more power, it can be too much for the stock splines and can strip them from the shaft.
The most common issue is at the hub/wheel end. If the car has to have any work done that involves taking the hub off, so suspension work, a new wheel bearing, that kind of thing, if the hub isn’t fitted correctly, it can damage the splines.
The CV joint
Drive shafts have a constant velocity joint at either end to allow the shaft to move with the suspension and steering of the car. These joints are packed with grease to keep them happy.
To keep all that grease in place, you have a CV boot, a rubber cover that flexes with the movement of the shaft. If this cover splits or comes adrift, dirt can get into the grease.
When that happens, the dirt grinds against the metal of the joint, eventually breaking it. If you get a CV boot advisory on your MOT, do not put it off. The £10 a new boot costs is a small price to pay when you consider that new drive shafts are hundreds of pounds to replace.
Replacing your drive shaft
Watch this video to see how it's done.
A very brief summary of the task:
- Remove the split pin from the hub nut, then crack the hub nut off so that it’s loose, but leave it attached.
- Jack the car up, remove the front wheels and take off the brake calipers. Remove the hub nut completely.
- Undo the nut onto the lower ball joint and break the hub assembly and the lower arm apart. Pull the hub away from the drive shaft, freeing the outermost end.
- Remove the drive shaft end from the gearbox.
- Fit the new drive shaft. Make sure you tighten the hub nuts up to the manufacturer's specified torque.